Glossaire Technique
Vous trouverez ci-après les définitions de termes utilisés dans les spécifications de ce catalogue et des conseils pour le choix et l’utilisation des capteurs de pression.
1/ DONNÉES D’ENTRÉE DU CAPTEUR
1-1 Gamme de Pression ou Étendue de Mesure (EM)
L’étendue de Mesure est le niveau de pression nominal pour lequel un capteur a été développé. Ce dernier doit être conforme à ses spécifications dans ce domaine de pression (la pression minimale est définie comme étant la pression de référence – cf 1-2).
Nota : Travail en fatigue
Certains capteurs peuvent être destinés à des applications de travail en fatigue, accélérant ainsi leur vieillissement. La durée de vie moyenne d’un capteur de pression standard est de 10 à 50 millions de cycles, 0 à 100% de la gamme de mesure. Il convient donc d’être particulièrement vigilant avec ces applications, car la durée de vie standard peut être très rapidement dépassée.
Exemple : un capteur subissant 1 cycle par seconde de manière continue, effectue ainsi 1.080.000 cycles pour une durée de 300 heures soit approximativement 12 jours.
Pour ces applications contactez-nous, nous avons des solutions à vous proposer.
1-2 Type
Quand un capteur mesure une pression, c’est toujours par rapport à une référence. Avec un capteur relatif, la mesure est réalisée par rapport à la pression atmosphérique du moment. Ainsi il doit toujours y avoir une connexion entre la pression atmosphérique et la partie sensible du capteur. Sur nos capteurs,
notamment pour les faibles étendues de mesure, cette connexion est assurée par un tube de référence, situé dans la sortie câble à l’arrière du capteur. Il convient cependant de tenir ce tube de référence dans un environnement sec, propre, non conducteur ou corrosif, sous peine de détériorer des composants internes du capteur.
Un capteur absolu mesure une pression par rapport au vide. La partie sensible est logée à l’intérieur d’un vide permanent. Dans nos capteurs, le vide est de 10-4 bar et scellé par bombardement électronique. Un tel capteur est étanche à l’air et l’eau (la partie sensible seulement). Ceci implique que le zéro électrique du capteur est directement liée à la pression atmosphérique du jour et varie avec elle.
Un capteur relatif scellé mesure une pression par rapport à la pression atmosphérique enfermée dans le capteur le jour de son scellement. C’est donc un capteur dont la partie sensible est étanche(à l’air et l’eau) et encapsulée non pas dans le vide mais dans la pression atmosphérique du jour de sa fabrication.
1-3 Surpression, Pression d’épreuve et pics de pression
La Surpression est la pression maximum à laquelle peut être exposé un capteur sans risque de dommage définitifs ou de modifications de ses spécifications. Dans notre fabrication, un test de surcharge (en général 150% de l’étendue de mesure) est appliqué à tous les capteurs.
La Pression d’épreuve est la pression pouvant être appliquée au capteur sans risque de fuite, mais créant des dommages irréversibles.
Si votre application comporte la mesure de “coups de bélier” successifs, il convient de protéger la membrane du choc provoqué par la rapidité de la mise en pression. Nous avons des solutions, contactez nous.
1-4 Impédance d’entrée (mentionnée seulement pour les capteurs non amplifiés)
L’impédance d’entrée d’un capteur sans électronique intégrée est égale à la valeur de résistance du pont de Wheatstone augmentée des résistances en série intégrées dans la compensation thermique du capteur.
1-5 Alimentation
Il s’agit de la tension recommandée par le fabricant et indiquée sur la fiche technique de chaque modèle, sous laquelle il convient d’alimenter un capteur. Il est conseillé d’utiliser une alimentation de qualité pour une mesure de précision surtout dans le cas des capteurs bas niveau (ex : PST161…).
Un choix important d’alimentations et de signaux électriques différents vous est proposé dans ce catalogue. Le tableau ci-après détaille la codification que nous utilisons et permet de déterminer rapidement à la lecture de la référence du capteur, le type d’alimentation et de signal correspondant au capteur retenu.
Notre Codification
Le dernier chiffre de la référence du capteur indique son type de signal électrique et par conséquence l’alimentation requise pour son fonctionnement.
Exemples de références de transmetteur : PTA224, PST165, PFD121
Veillez à bien respecter le câblage de nos capteurs (code couleur et câblage de nos connecteurs fournis).
La majorité de nos capteurs est protégée contre les inversions de polarité, certains contre les surtensions : ces données sont indiquées sur les fiches techniques individuelles.
N’appliquez jamais la tension d’alimentation aux bornes “mesure” du capteur, vous l’endommageriez définitivement.
2/ DONNÉES DE SORTIE DU CAPTEUR
2-1 Impédance de sortie (mentionnée seulement pour les capteur non amplifiés)
Pour les capteurs bas niveau (sans électronique intégrée), l’impédance de sortie est sensiblement égale à la valeur nominale des résistances constitutives du pont de Wheatstone.
2-2 Déséquilibre ou Signal de sortie 0%
C’est le signal électrique délivré par le capteur, alimenté sous la tension recommandée et soumis à sa pression de référence ; soit la pression atmosphérique pour les capteurs relatifs et le vide pour les capteurs absolus. C’est donc le signal de sortie du capteur à 0% de son étendue de mesure.
Nota : Pour les capteurs absolus, le déséquilibre peut être sur demande réglé à la pression atmosphérique.
2-3 Signal de sortie à 100%
Il s’agit du signal électrique délivré par le capteur, alimenté sous la tension recommandée et soumis à la pression nominale, soit 100%, de son étendue de mesure.
Code Signal électrique Alimentation requise pour le capteur
1 Signal bas niveau : 1 à 3mV/V Alimentation 10Vdc stable et régulée
2 Signal bas niveau : 5 à 10mV/V Alimentation 10Vdc stable et régulée
3 Sortie tension ratiométrique : 0,5 à 4,5V Alimentation 5Vdc ±0,05 stable et régulée
4 Sortie tension : 0,5 à 4,5V, 0-5V ou ±5V Alimentation non régulée de 9,5 à 27Vdc
5 Sortie courant : 4-20mA Alimentation non régulée de 12 à 27Vdc
6 Sortie tension : 0-10V Alimentation non régulée de 15 à 27Vdc
7 Sortie tension : 0,5 à 4,5V Alimentation non régulée de 8 à 16Vdc
2-4 Précision
L’écart de linéarité est le plus grand écart entre la courbe d’étalonnage du capteur et une ligne droite appelée “meilleure droite” représentée par la droite 0-100% EM ou la droite des moindres carrés. Cet écart s’exprime en pourcentage de l’étendue de mesure.
L’hystérésis est la différence des indications du capteur lorsqu’on atteint une même valeur de la grandeur mesurée par variation croissante continue ou variation décroissante continue. Elle est égale à la moitié de l’écart maximal constaté. Elle s’exprime en pourcentage de l’étendue de mesure.
La non répétabilité est la différence de signal capteur constatée par application d’une même pression plusieurs fois consécutivement dans les mêmes conditions (température, pression croissante ou décroissante…). Elle peut ainsi être déterminée en réalisant deux étalonnages consécutifs et s’exprime en pourcentage de l’étendue de mesure (% EM).
La non linéarité, l’hystérésis et la non répétabilité constituent l’erreur statique (NL+H+R) du capteur, c’est-à-dire son erreur à température ambiante (d’étalonnage).
2-5 Fréquence Propre de la Membrane
La fréquence propre de la membrane est la fréquence à laquelle l’élément sensible du capteur entre en résonance et répond avec un déplacement maximum à une contrainte spécifique appliquée. Elle est également appelée Fréquence de Résonance.
Soumettre un capteur à des contraintes dont la fréquence est supérieure à sa fréquence propre peut endommager le capteur.
La fréquence de résonance de la partie sensible est directement liée à la technologie utilisée et permet de classer les capteurs en 3 catégories distinctes : capteurs de pression statiques, légèrement dynamiques ou dynamiques.
Les capteurs à Technologie Couche Mince sont considérés comme des capteurs dynamiques.
Pour des mesures hautement dynamiques, nous vous invitons à sélectionner un capteur non amplifié (notre codification 1 et 2) et à membrane affleurante ou quasi affleurante.
Les fréquences de résonance de nos capteurs sont indiquées dans les spécifications et sont également variables selon les étendues de mesure.
2-6 Temps de Réponse et bande passante
A partir d’un échelon unité représentatif de l’étendue de mesure du capteur, le temps de réponse est le temps mis par le capteur pour délivrer le signal correspondant à 100% de l’échelon unité. Le temps de réponse est généralement exprimé en millisecondes.
Pour les capteurs amplifiés (à électronique intégrée ou déportée), le temps de réponse est limité par l’électronique, incluant ou non des filtres.
Sur nos transmetteurs standards à sortie analogique, le temps de réponse est de l’ordre de 10 ms. Nous pouvons, sur demande, ajuster ce temps de réponse dans les limites indiquées sur chaque spécification, généralement de 1 à 100 ms.
Pour ce qui est des transmetteurs à sortie numérique, le temps de réponse est de l’ordre de 10 ms.
La bande passante correspond à la plage de fréquence dans laquelle le signal capteur restitue la véritable amplitude et la phase du mesurande. (correspond environ à 20% de la fréquence de résonance à -3 dB soit ± 6%).
2-7 Résistance d’Isolement
C’est la résistance mesurée entre deux points du capteur, sous une tension continue (en général 50Vdc) à température ambiante.
3/ ENVIRONNEMENT DU CAPTEUR
L’environnement dans lequel le capteur fonctionne doit être défini et mentionné lors de la commande afin, si besoin est, d’adapter le capteur lors de sa fabrication. Nous listons ci-après les éléments principaux qu’il convient de prendre en considération. Si certaines conditions de votre application diffèrent des spécifications du capteur sélectionné, contactez-nous pour que nous déterminions ensemble les options nécessaires à mettre en oeuvre.
3-1 Températures de compensation et d’utilisation.
A quelles températures (minimum et maximum) le capteur sera t-il utilisé ?
Entre ces deux limites (température d’utilisation) quelle est la plage dans laquelle le capteur doit être le plus précis (température de compensation) ?
La température d’utilisation est la plage de température pour laquelle le capteur peut fonctionner sans dommages.
Exposer le capteur à des températures supérieures ou inférieures aux limites du domaine d’utilisation peut endommager irrémédiablement celui-ci.
Le domaine de compensation en température est la plage de température dans laquelle les caractéristiques de dérives de zéro et de sensibilité en température du capteur sont conformes aux spécifications. Le capteur continuera de fonctionner dans les limites du domaine d’utilisation en température avec des performances qui pourront s’écarter progressivement des spécifications d’usine. Le capteur a été compensé pour des paliers de températures stables et non pour de brusques variations de température ou chocs thermiques. Si une variation rapide se produit, il faut laisser le temps au capteur d’atteindre l’équilibre thermique avant qu’il réponde aux spécifications données. La température de compensation standard de nos capteurs de pression est de 0 à +60°C (utilisation de –40 à +125°C).Vous disposez selon les modèles des options suivantes :
•-25°C à +85°C
• -25°C/+125°C
• -40°C à +125°C
• 0°C à +150°C ou 175°C
• +20°C à +260°C pour les modèles haute température.
Nous pouvons cependant vous fournir un capteur compensé dans un domaine de température propre à votre application. Consultez-nous.
Température du fluide
Un capteur peut être soumis à une température modérée (40 à 60°C par exemple) alors même que le fluide mesuré est à une température autre (négative ou positive). Dans ce cas, il convient de spécifier ces deux températures lors de votre commande, pour nous permettre de vous fournir un produit adapté, garantissant une mesure de précision.
Flux thermique directif
Lorsqu’un capteur est sujet à des flux thermiques directifs chauds ou froids, intermittents ou continus, cela induit des variations de température pour ses composants internes. Ces variations sont difficilement compensables dans le cas de capteurs miniatures. Il convient de protéger les capteurs de ce type de phénomènes par une barrière thermique ou une ceinture de protection.
3-2 Dérives thermiques
La dérive thermique de zéro en température est la variation du déséquilibre en fonction de la température, dans le domaine de compensation. Cette dérive de zéro n’est pas une fonction linéaire. La dérive thermique de sensibilité est la variation de la sensibilité avec la température dans la plage de compensation. Contrairement à la dérive de zéro, elle présente un aspect généralement linéaire. Ces dérives sont exprimées en pourcentage de l’étendue de mesure par degré °C pour des variations de température à l’intérieur de la plage de compensation.
Nota : Ces spécifications sont données pour des variations thermiques progressives. Une variation rapide de température peut momentanément provoquer une dérive thermique de zéro supérieure aux tolérances. Il convient d’attendre la stabilisation du phénomène thermique afin de laisser les éléments de compensation agir.
Pour un certain nombre de capteurs nous spécifions des dérives thermiques du zéro et de la sensibilité cumulées. Il faut considérer que la tolérance donnée (±0,02% EM/°C par exemple) est la valeur maximale que peut atteindre la somme des dérives du zéro et de la sensibilité, dans le domaine de compensation.
3-3 Sensibilité aux accélérations
Certaines mesures de pression sont effectuées sur des éléments soumis à des accélérations, des vibrations ou des chocs. C’est le cas des capteurs miniatures utilisés dans certaines applications embarquées (automobile, aéronautique, spatial…).
Nous avons développé nos capteurs de pression pour qu’ils soient les plus insensibles aux accélérations, chocs et vibrations.
La sensibilité à l’accélération correspond à une tension parasite mesurée en sortie du capteur de pression causée par l’effet de l’accélération sur la membrane du capteur. Les valeurs nominales sont données dans les spécifications propres à chaque modèle.
3-4 Stabilité long terme
La dérive à long terme est la variation de signal d’un capteur dû au seul effet du temps. Elle permet de caractériser sa stabilité et est exprimée en pourcentage de son étendue de mesure pour une période donnée (en général 1 an).
4/ INTERFACES DU CAPTEUR
Un nombre important d’interfaces mécaniques et électriques vous est proposé dans ce catalogue. Pour chaque capteur nous mentionnons les différentes options de raccordements disponibles.
Dans les fiches techniques détaillées de chaque modèle, vous composez votre capteur avec son raccordement mécanique et sa connexion électrique. Vous pouvez ainsi déterminer son encombrement spécifique en additionnant les dimensions des trois composantes :
• la longueur du raccord mécanique
• la longueur du corps du capteur
• la longueur de la connexion électrique
4-1 Raccordement mécanique
Couple de serrage et étanchéité
Reportez-vous aux montages mécaniques que nous vous conseillons de réaliser pour chaque type de raccord capteur. Nous vous indiquons également le type de joint fourni pour chaque raccord. Le filetage ne doit pas être serré sous peine d’engendrer des contraintes mécaniques et thermiques préjudiciables
au capteur. Le couple de serrage dépend du joint utilisé, du raccord mécanique et de la gamme de pression du capteur.Veillez à bien respecter les couples préconisés sur nos fiches techniques.
Nous avons développé un certain nombre de raccords mécaniques spécifiques qui présentent des avantages, très appréciables dans certaines applications :
• Le raccord par bride permet de s’affranchir des effets du couple de serrage et garantit un très bon maintien dans les applications à fortes vibrations.
• Le raccord double bagues Swagelok® et les raccords avec cône permettent une étanchéité sans joint, métal/métal, particulièrement adapté pour les fluides agressifs. L’étanchéité est ainsi fiabilisée dans le temps.
Joints toriques
Veiller au bon montage du joint, à sa bonne qualité et à son changement régulier. Le joint Viton est souvent recommandé pour sa tenue aux fluides et à la température. Liste des matériaux de joints toriques avec leur domaine de température et compatibilité avec différents fluides.
Vibrations et montage
Dans le cas de vibrations importantes, il est recommandé de bien maintenir le capteur et le câble afin de limiter la contrainte au niveau de l’embout du capteur. Pour le choix d’un capteur, orientez-vous vers les produits « pour environnements difficiles » ou vers les capteurs miniatures et ultra miniatures qui ont été développés spécifiquement pour des applications « embarquées » ayant d’importantes contraintes vibratoires et thermiques.
4-2 Connexion électrique
Effectuer un raccordement rigoureux y compris de la tresse métallique (cas des sorties électriques par câble), de la borne terre ou du corps du connecteur (cas des connecteurs).
Matière Fluides Température
Silicone Air chaud, Oxygène, huile, liquide de frein -70°C à +230°C
Buna Huile, essence, lubrifiants, détergents -35°C à +80°C
Néoprène Fréon, compounds, oxygène à basse pression -40°C à +120°C
Ne pas utiliser avec des huiles minérales
Viton Fréon, butane, huiles minérales, hydrauliques et silicones, nombreux acides -18°C à +210°C
Fluoride-Silicone Solvants à base de chlore, huile, essence, air chaud -65°C à +180°C
Ethylène-Propylène Vapeurs, savon -54°C à +135°C
RÈGLES GÉNÉRALES POUR LA MISE EN SERVICE DE NOS CAPTEURS ET TRANSMETTEURS :
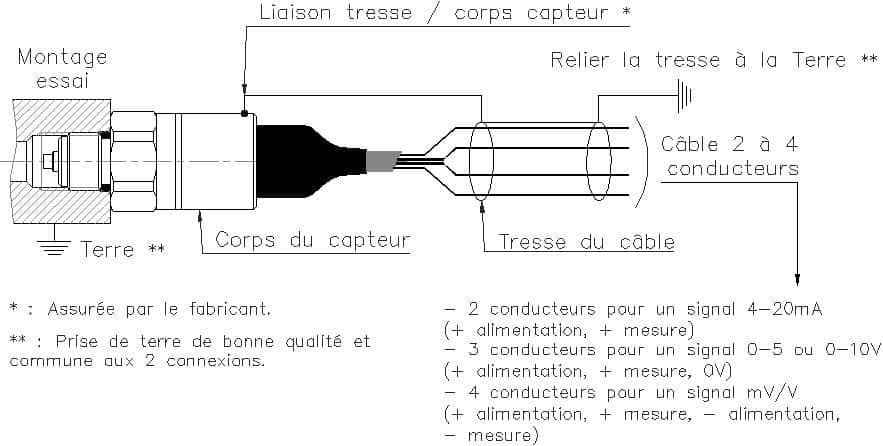
– Utiliser une terre de qualité, sans création de courant de circulation.
– Respecter les équipotentialités.
Nota :
1 – Dans le cas d’environnements très bruités, utilisez notre câble PVC double blindage particulièrement adapté. Préférer également les connexions électriques par câble aux connecteurs, toujours plus exigeants de mise en en oeuvre.
2 – Eviter le côtoiement du câble capteur avec d’autres câbles, la proximité de câbles haute tension, câble de relais de puissance, câble de puissance…
4-3 Compatibilité électromagnétique (CEM)
Nos transmetteurs ont été testés dans des laboratoires accrédités et sont conformes aux normes CE.
Dans le cas d’applications nécessitant une certification spécifique, notre bureau d’études peut mener avec vous une homologation de capteur.
4-4 Matériau
Nous spécifions les matériaux utilisés pour les corps et parties sensibles de nos capteurs. Il s’agit pour les modèles standards d’acier inoxydable (15-5PH, 17-4 PH et 316L) ou de Titane (TA6V).
4-5 Indice de protection
La grande majorité de nos capteurs sont IP65 ou IP67. Il convient de noter que si un capteur doit être utilisé à l’extérieur, une sortie électrique par câble est généralement plus adaptée aux variations climatiques, aux projections et plus résistant dans le temps qu’un connecteur, sauf connecteurs étanches. Ces derniers sont généralement chers et difficiles à monter sur nos capteurs (voire impossible sur les capteurs miniatures) et très long en approvisionnement.
Si vous utilisez des capteurs dotés de connecteurs intégrant des joints (connecteurs DIN 43650 par exemple), pensez à changer régulièrement le joint interne du connecteur. L’indice de protection de votre capteur en dépend.
4-6 Joint interne
Si la fiche technique du capteur indique qu’il n’y a aucun joint interne au capteur, cela signifie que la partie sensible du capteur est soudée sur l’embout de pression et mise, sans séparateur, directement en face du fluide. Cette membrane est en Acier inoxydable 17-4PH ou en titane TA6V. C’est le cas de la très grande majorité de capteurs, compatibles avec la plupart des fluides.
Dans certains cas, rares, nous indiquons la présence et la nature du joint utilisé. Il convient de vérifier la compatibilité de votre fluide avec le joint. Si votre application le nécessite, nous pouvons sur demande, pour l’ensemble de nos capteurs, fournir une membrane soudée, sans joint interne.
4-7 Compatibilité des capteurs avec les différents fluides
La compatibilité d’un capteur avec les fluides couramment utilisés par l’industrie est essentiellement liée à sa technologie, c’est-à-dire au type de partie sensible en contact avec le fluide et à son mode de raccordement (avec joint, type swagelok…). Les matériaux des capteurs sont indiqués sur les fiches techniques.